LKAB produces Apatite from mine waste in a new pilot plant
Leif Boström, Senior Vice President for Business Area Special Products and CEO of LKAB Minerals, which is managing the development within LKAB, explains “We are now up and running with the first step, to produce apatite concentrate, although in a pilot scale. We need to test, verify and plan this production thoroughly to obtain the right yield and cost of production. Additionally, we are planning for a production that is energy efficient and carbon dioxide-free.”
Mobile pilot plant
The pilot plant is built on container platforms to allow it to be moved within and between LKAB’s production plants in Malmberget and Kiruna, in Northern Sweden. Tests with tailings sand (waste material which is a by-product of mining) from the two mines and the respective processing plants will be carried out in campaigns. Right now, a production campaign is underway in Malmberget. The process has multiple steps, flotation is the key principle applied to separate the apatite from the non-valuable tailings. This process is repeated in several steps to obtain a high purity product with the right specification for further processing.
Innovative chemical processing
The further processing will be done using innovative chemical processing, that LKAB is working intensively to develop. Here, the apatite will be processed into phosphorus mineral fertilisers, rare earth elements, fluorine and gypsum. The EU lists both Phosphorus and REEs as Critical Raw Materials. This is due to their high economic importance and our import dependence. But right now, Leif Boström is pleased to be able to inform of the successes with the apatite production that is the needed first step.
Critical raw materials
”We estimate that a full-scale production from Malmberget and Kiruna will produce around 400,000 tonnes of apatite concentrate annually, in two plants that will be of similar size to our existing iron ore concentrating plants. When we can be up and running depends on the technical developments and the pre-engineering. Also, this will rely heavily on external factors such as environmental permits. Our objective is to recycle our mine tailings to critical raw materials, and the sooner the better” Leif Boström concludes.
Press images:
Top image: Graphic, process description, Graphic: Anders Humlebo/TT Nyhetsbyrån
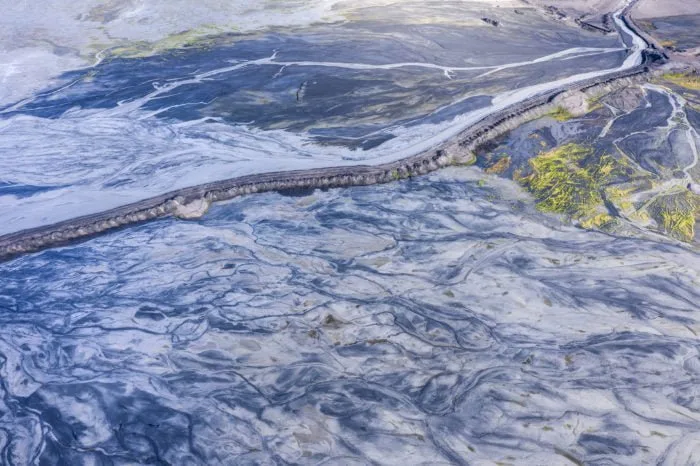
Photos, aerial and from the pilot plant, Photo: Fredric Alm
Graphic and photos are free to use in editorial material about the ReeMAP project. However, please make sure to include graphic/photo credit.
ReeMAP – Turning today’s waste into tomorrow’s resources
We constructed the project name from two of the main products we aim to recycle from our tailings sand, REE’s (Rare earth elements) and MAP (a phosphorus mineral fertiliser product). The EU considers both to be critical raw materials.